Overhauling Andrew Feathers Cannondale SuperSix Evo
It dawned on me that if we could convince him to allow us to ‘update’ this ageing bike by using the robot we could make it super light and competitive again for the 2024 championship! We could deliver him one of the lightest bikes ever made and share it with the world but would he be prepared to have a go?
Creating the ultimate ‘FEATHERLITE’ bike with Robotics
‘What do you mean you have a robot. What does it do?’ Obviously it is not an everyday question so I was compelled to explain the proposal. ‘Basically over 2 years we have designed and built a one-off amazing piece of equipment which is able to follow precise scans of bicycles down to 0.03mm, that if we chose to, could modify any bike shape put before it. But first the bike in question must be 3d scanned to create the digital bike in order for the robot to do what we wanted to the frame. In other words Andrew… we want to shed some fat off your bike!’ ‘Oh yes please!’ Came his immediate answer over the phone. ‘When can I come over?’
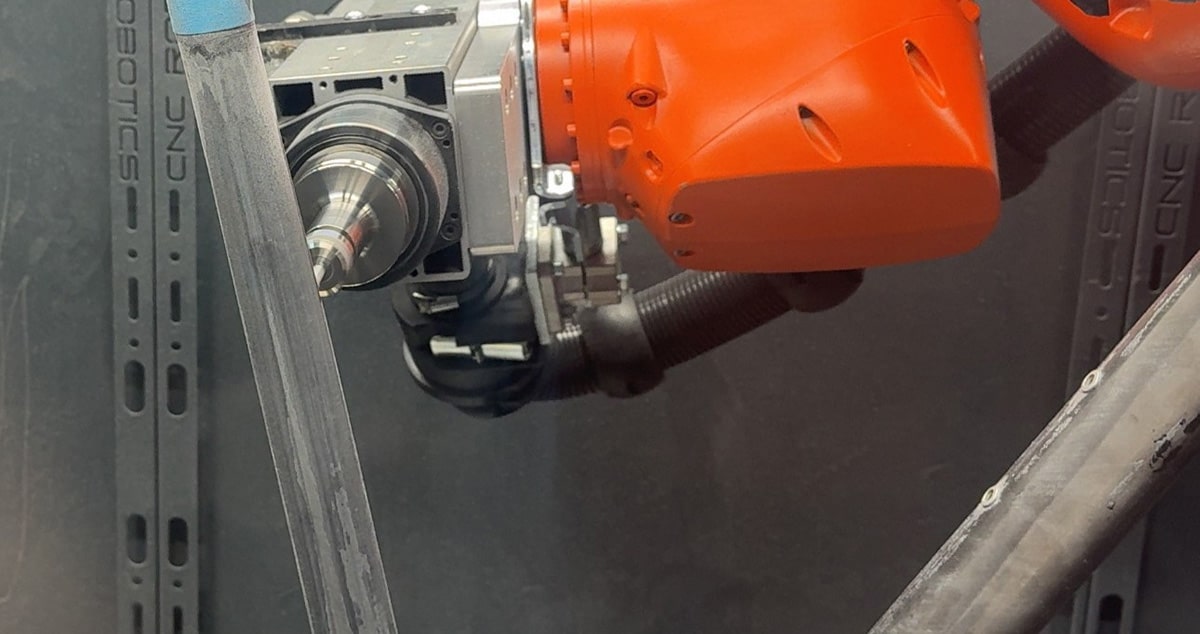
The fact was we had never done this before but if we are conservative with material removal the robot could certainly execute this procedure on Andrew’s bike. It was an opportunity for the industry to better understand that if you repair by robot, the results are very impressive indeed but more importantly can guarantee the outcome consistently.
What is the point of the robot, is it just a marketing tool as some critics have suggested? Well I have some rather sobering news for repairers now and in the future. Carbon bikes have halved in weight on average within the past 4 years. As a result wall thicknesses have reduced to as little as 0.4mm in the mid tube sections. Although very stiff they are more susceptible to impact fractures than at any time in the past. The technology utilised to manufacture a high end carbon bike is now simply too advanced for a hand repairer. As skilled as the traditional carbon repairer might be, the idea that reshaping these advanced bikes in the name of ‘safe repair’ without knowing is simply too risky
But how then can we safely replace and reshape the carbon without the mould itself
Only the mould would guarantee the accuracy of the replacement carbon right? The scanned bike is the mould upon which the robot contours. Let me explain simply: The frame is the positive result of the mould is it not? Then the scan of the frame replaces the need for the mould? If the robot can see the mould shape now then what ever we instruct it to do it will. For example: We can remove material to within 0.03mm of the wall thickness thus providing the basis for the inner material limit. Once cured the mould shape is simply reprofiled back to the original shape.
In fact it is so accurate that if we only wanted the clear coat removed off the surface and not the colour pigment on an existing section it will do just that!
For the first time we can ensure every repair remains true to the original specifications. This is critical to achieve if the bike is to remain in symmetry with itself. A safe repair is an invisible repair. This scan/ robot repair system is no marketing tool.
Andrew’s bike was paint stripped and structurally inspected to plot the safest process. We decided as this was already a HighMod SuperSix model that we could only remove material across the top tube and the downtube. A cutting depth of 0.1mm was initiated and the process took roughly 40min to complete. Unfortunately not all was well when we discovered tiny break throughs on the mould seam line located on the underside of the down tube. In fact we found several voids on this seamline which was a shock considering the amount we removed. Unfortunately we had to add weight by re-enforcing with carbon the length of the underside seam line. Fortunately with the robot we could reprofile the tube to where we wanted it.
We wondered if this exercise was not going to make much difference in the end but even after the frame set was lightly repainted with the most attractive naked bronze finish we decided to wait for Andrew to collect before we could weigh it together. To our relief we were surprised to see that 200g had still been shaved off the existing frame and 80g off the forks making it the lightest Cannondale ever!
Good luck Andrew with the up-and-coming hill climb. Only our reputation is on the line.