What are the Pros and Cons of modern bikes then?
Many brands are customer lead which is not always a good idea in industries such as automotive, aviation motorcycling and cycling. In aviation there is a very robust safety and procedure culture in place which is engineer lead. Cycling was largely unregulated if it were not for organisations such as the UCI who’s prime function is to ensure fair play and ensure the tools of competition are fit for purpose. This organisation has a huge affect on all manufactured cycling product both directly and indirectly. In fact non-UCI competition see all kinds of interesting craft in Iron-man. This ‘open-forum’ is the breeding ground for future designs which also indirectly puts pressure on the UCI for example weight restrictions of 6.8kg at the time of writing.
If you imagine a Specialized Aethos frame weighting in a just over 600g it is no wonder there is so much criticism toward the UCI’s seemingly backward approach to introducing more current specs into the completion but maybe they know something we don’t appreciate. For example the 6.8kg weight restriction (build bike) was introduced in 2000. I can attest to the fact that todays carbon bikes do not look even vaguely the same nor are they manufactured in the same way.
Tests back in 2000 showed the UCI officials that 6.8kg was the minimum weight the frames could be deemed safe from structural collapse. If you think that in those days all carbon bikes were hand bonded carbon frames. Bottom brackets were woefully thin as were the chain sets causing these frames to be very flexible and heavy in comparison to the aluminium predecessors.
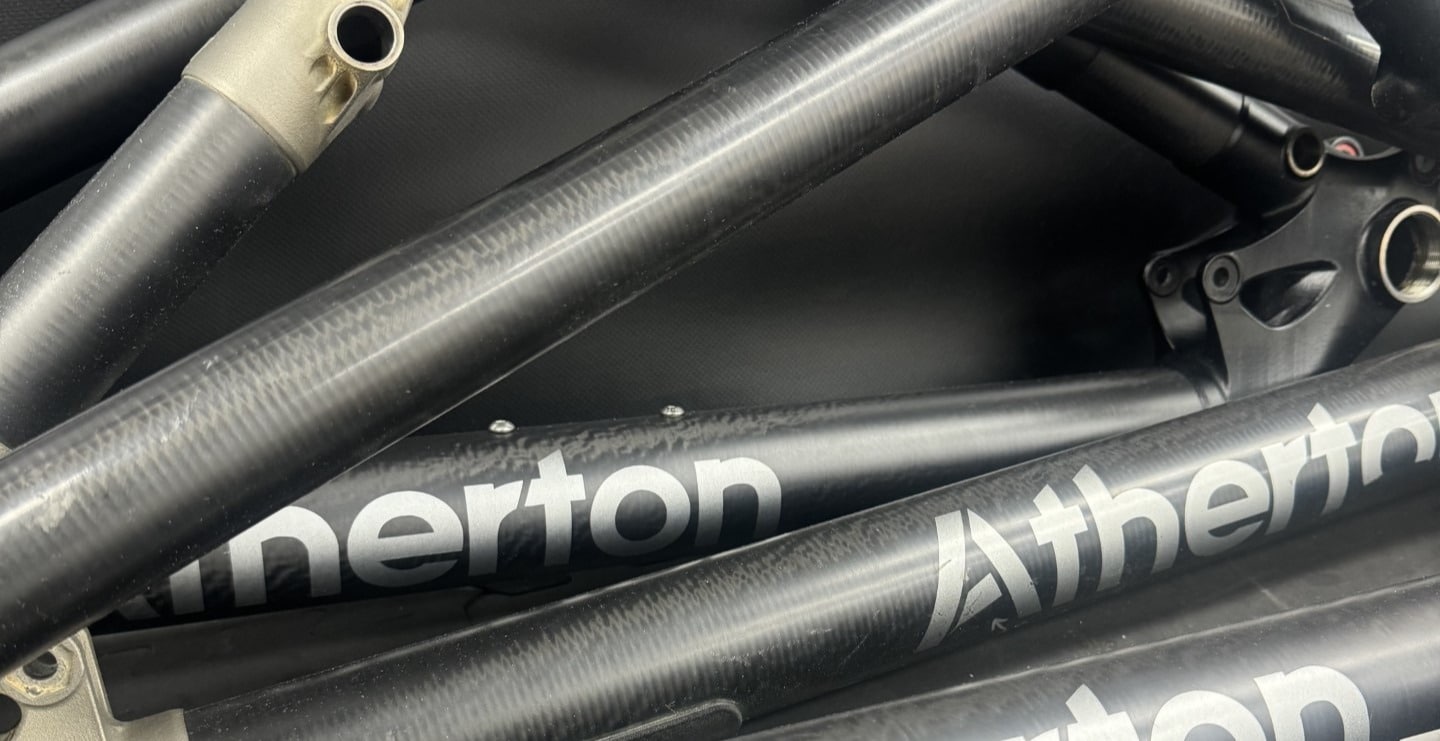
Manufacture processes have improved as brands understand what has gone wrong in the past. For example you will see very few alloy and carbon components mated and bonded together. These two materials are incompatible with each other as the alloy expands and contracts at a different rate to carbon which is a lot more stable. The epoxies used simply failed over time. Warranties covered joints where frame sets were bonded together by hand to make a ‘ monocoque’ frame when in actual practice only now are we seeing true monocoques appear. The difference is notable in that these true ‘monocoques’ are connected together by carbon laminate and not as sections held together by epoxy. We as repairers see 70% less mid tube manufacture failures compared with the past so these modern warranties reflect this improvement.
With the advent of disk wheels we can now see the challenges of awful rim brake concepts being thrown out in favour of non wearing rims or alloy/ carbon wheels. The other improvement in carbon bikes are the through axil systems as opposed to quick release dropouts which was a hangover from pure alloy bikes. Alloy being the best material for this system but a disaster for carbon.
Most of these modifications are largely borne out of the cost of warranty replacements but not in the name of progress.
So what is not so good about modern bikes then? I equate most my criticism to design memory. Bike companies are renowned for lower pay design jobs and/or a stepping stone to bigger things. This has an affect on the legacy of good designs and the reasons they were implemented in the first place. When new designers make their mark I believe this is where some good ideas are not re-considered because they are ‘old.’
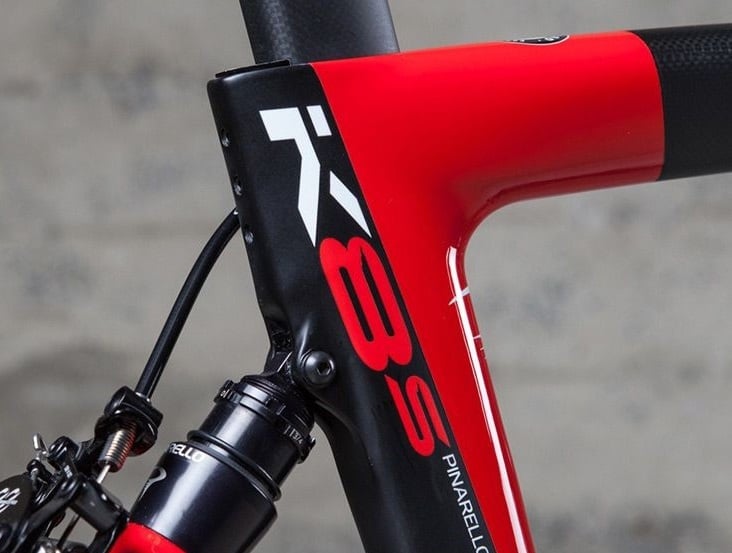
Lets look at a not so obvious example – The rear seat stay position on the seat tube. The ‘old’ style was to junction the top of the stays at the same height as the top tube junction with the seat post clamp. It is obvious to me that this traditional geometry allowed the seat tube to flex and pivot at this junction providing much needed relieve and even a form of suspension. But because TT bikes, in particular, look ‘racey’ because the geometry of the stays are low down for aero reasons the simply assume that we can sell more aero road bikes which look this way when in fact we are applying designs to a different discipline with little to no regard for the different conditions in which the road bike operates.
Some brands looked really hard at this fatigue issue as an advance by introducing flexible junctions while other brands simply ignored this, in fact, locking off any flexibility by lowering the seat stays and extending them into the top tube to boot! Now I cannot claim to be a successful bike designer but I can say this: As a multi brand repairer who mainly specialises in bikes which have already been produced, it is astonishing to me how we are still seeing such fundamental errors not seen in aerospace or automotive industries.
That said I believe the level of manufacturing skill in carbon bikes as far and material application and processing is far advanced compared with other industries such as F1 even. I have seen both and my view remains unwavering. If we could enlist the pro-cyclist team leader with an F1 engineer in design with the skills of a bike manufacturing engineer then we would most likely set a standard to beat for a long time but sadly this is not the motivation for the bike brands. They need to shift stock as best they know how. By changing and re-inventing good and bad ideas keeps the industry moving but ‘forward’ maybe not so much.
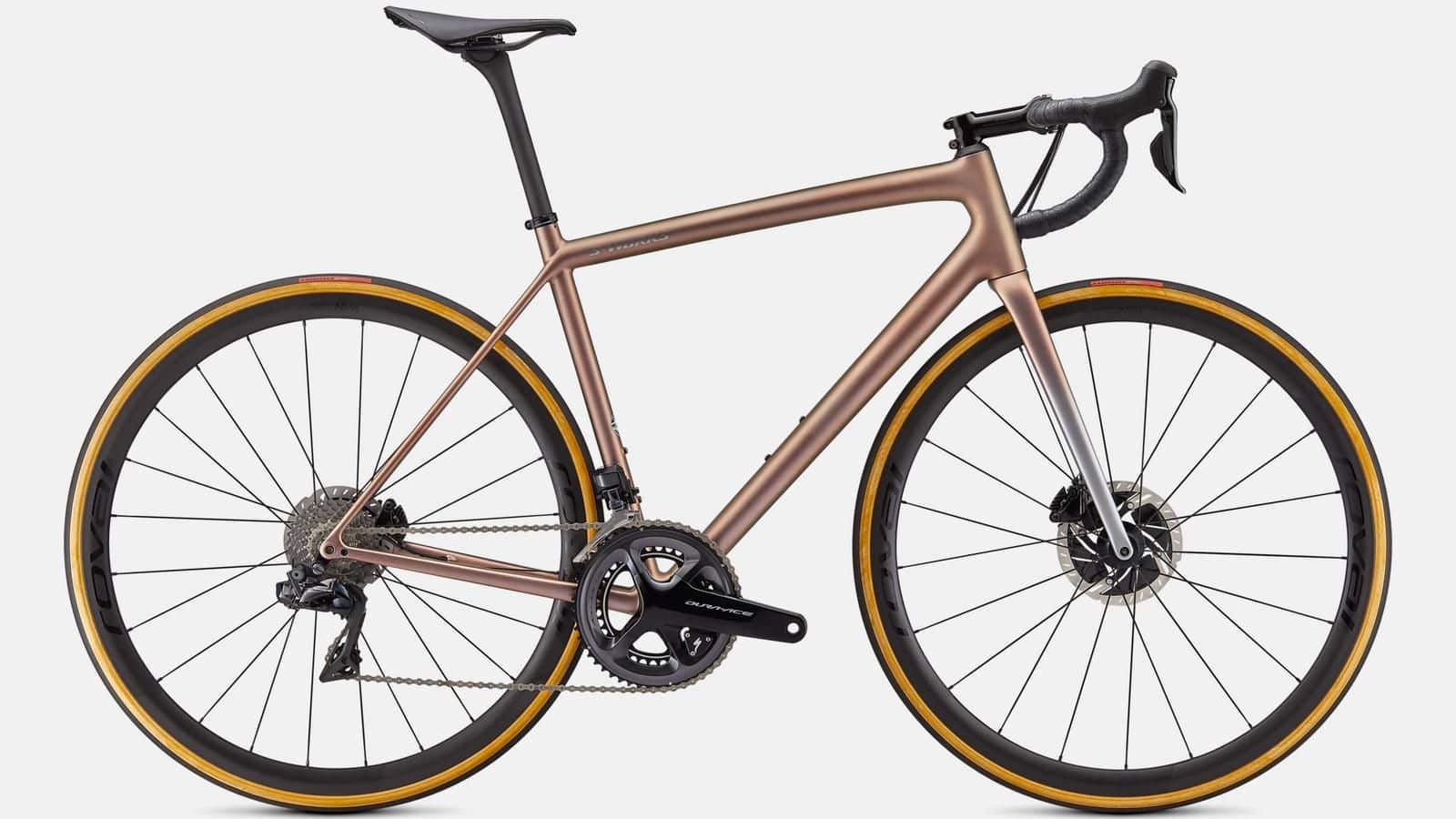
What do I think modern bikes are better at?
BB stiffness. Dialled in construction methods and weight reduction in bikes which specialise in climbing.
What do I not like about modern carbon bikes?
Ultra light weight bikes. Other that for hill climbing they do not have a comfortable function in the other 2 elevations. They are more ‘throw-away’ in longevity yet the price tags are higher than ever. Appalling after care service for high end road bikes. The inappropriate application of carbon in bike components better suited to other materials such as fork steerers.
What do I like about older carbon bikes?
Reasonable frame weight and robustness in the mid tube sections. Geometric traditions determine the best positions over time. We have not evolved as humans.
Against?
Poor understanding of carbon fibre and bikes. Inefficient understanding of bonding incompatible materials together. Caught up in the legacy of alloy bikes particularly interfaces such as dropouts, clincher wheels and rim brake systems.
So what does the future look like?
Well it seems to look a bit depressing if I am honest. As if the industry is not already legislated to comply with the ever stringent green agenda you are going to find a slight backward progression in the construction results of carbon bikes as I see the tech today. What do I mean? Well its all about recycling at the end of the day. Apparently thermoset (chemical setting carbon laminate) is not environmentally friendly. Thermoset (heat setting) is. The issue I have with thermoplastic is that it requires a lot more actual energy and material to produce a comparable carbon bike and then we are still not sure how you can recycle a spent bicycle in any useful way. Both can be ground to powder and reused using both thermoset and thermo plastic into by products such as components for bikes and other things.
To assume thermoplastic is more environmentally friendly is not the case but lets see. Some companies are embracing 3d robotic printing of rather interesting frames sets which are not restricted by traditional mould processes so we wait and see but my opinion is that there is no better marriage between carbon fibre and bicycles in any product range I can think of both in weight structural rigidity and cost.
Let us not forget that if we are talking about the environment then carbon bikes are infinitely repairable too!