Founded on the principle of extending the lifespan of carbon bikes through expert repair and refurbishment, Carbon Bike Repairs has revolutionised the cycling industry. This case study looks into their innovative approaches, strategic decisions, and the impact it has made on both cyclists and the environment.
Technology to repair Technology
In the world of cycling, carbon fibre has emerged as the material of choice for its unmatched strength-to-weight ratio and aerodynamic properties.
From developing proprietary repair techniques to fostering partnerships with leading bike manufacturers, Carbon Bike Repairs has navigated the complex landscape of carbon fibre repair. Through meticulous attention to detail and a commitment to quality, the company has earned the trust of cyclists worldwide, establishing itself as a beacon of reliability in an industry characterised by constant innovation.
The overall objective for adopting 3D scanning was to elevate the repair and customisation services offered, to increase customer satisfaction and efficiency, and give a competitive edge by assisting to provide the following:
Precision Repairs: Accurately capture the geometry and contours of damaged bike parts, to ensure that the repaired parts fit seamlessly with the original structure, maintaining the integrity of the bike.
Quality Control: By scanning both before and after repairs, to ensure that the repaired parts match the original specifications. This helps in quality control, ensuring that the repaired bike parts meet industry standards and customer expectations.
Time Efficiency: Reduce the time required for measurements and design. Instead of manually measuring each part, technicians can simply scan the damaged area and quickly generate a digital model, expediting the repair process.
Reduced Waste: Accurately assessing the extent of damage minimises material waste. This is particularly important with carbon fibre, as it’s expensive and excessive material removal can weaken the structure.
Archiving and Documentation: To create a digital archive of bike models and repairs, which can be used for future repairs, warranty claims and creating digital records for customers.
Advanced Analysis: Obtain detailed data about the bike’s structure, so it can be used for advanced analysis, including stress analysis, fatigue testing, and aerodynamic simulations, enabling specialised services like performance optimisation to be offered
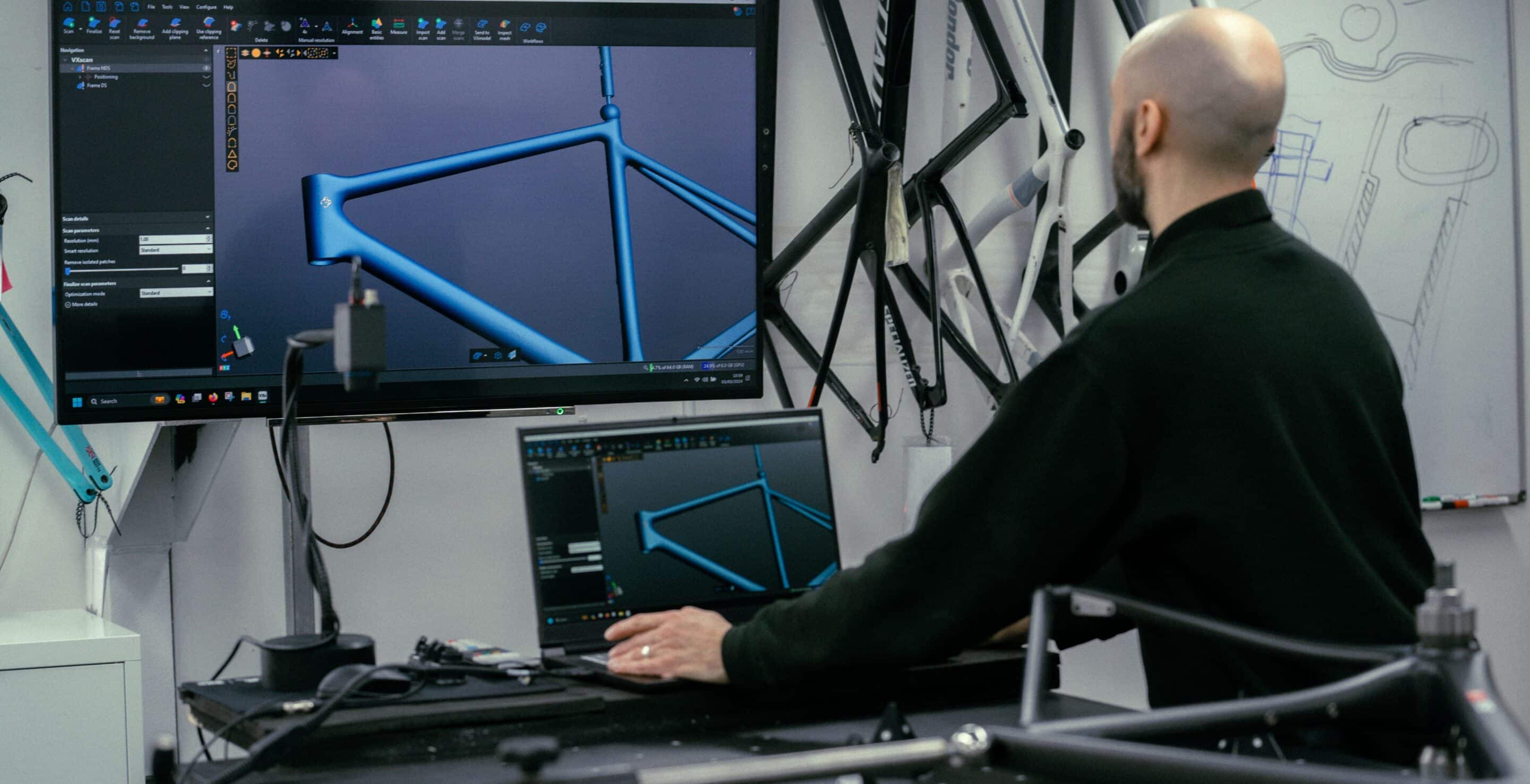
Challenge
Repairing carbon fibre bike frames presents unique challenges due to the complex structure of the material and the need for the utmost precision, it also requires meticulous attention to detail, especially in maintaining the frame’s structural integrity and original geometry.
Traditional repair methods often struggle to achieve the level of precision required for optimal performance and
safety, which is why Carbon Bike Repairs looked to find an alternative solution for their repair process and adopted
3D Scanning technology as an integral part of it to ensure increased accuracy and quality of repairs.
Vision
Carbon Bike Repair envisioned a solution that would streamline their repair processes, enhance accuracy, and ultimately deliver superior-quality repairs to their customers. They aimed to integrate cutting-edge technology that could optimise their workflow and ensure consistent, high-quality outcomes setting a new standard in carbon fibre frame repair, providing cyclists with durable and reliable solutions.
Application
The Creaform HandySCAN Silver was introduced into Carbon Bike Repair’s workflow to revolutionise their repair processes. This advanced 3D scanning technology allows for precise measurements and comprehensive inspections of damaged bike frames, enabling technicians to identify even the smallest imperfections.
Carbon Bike Repair utilises a unique re-construction process for their frame repairs, setting them apart from traditional repair shops. Unlike the majority of carbon frames that are repaired without the bikes specifications, CBR’s frames are reconstituted by replicating the exact mould to deliver an x-ray invisible restoration with a lifetime warranty that is valid
The Repair Process
The repair process at Carbon Bike Repair begins with scanning two frame sets using the Creaform HandySCAN Silver. This allows for accurate measurement and comparison of geometry between frames.
The HandySCAN Silver provides detailed data, ensuring precise replication of the original frame geometry
Benefits
Precision: The HandySCAN Silver provides precise 3D measurements, allowing technicians to assess damage and execute repairs with unparalleled accuracy.
Efficiency: By streamlining the repair process, the HandySCAN Silver reduces turnaround times, enabling Carbon Bike Repair to deliver repairs to customers faster.
Quality: The use of advanced technology guarantees the highest standard of repair, enhancing the durability and safety of repaired frames.
Versatility: The portability and versatility of the HandySCAN Silver allow technicians to perform scans in various
environments, making it an invaluable tool in the repair workshop.
Innovation: Carbon Bike Repair’s adoption of the HandySCAN Silver demonstrates its commitment to innovation and excellence within its industry
The Final Outcome
With the integration of the Creaform HandySCAN Silver into their processes, Carbon Bike Repair has achieved remarkable improvements in efficiency, accuracy, and quality. Their ability to deliver superior repairs to customers has strengthened their position as a leader in the industry, while also enhancing customer satisfaction and loyalty.
Writers Credit: Leigh Edwards from MSL 3D Scanning