Carbone ou thermoplastique, quelle est la meilleure solution ?
La fibre de carbone est souvent considérée comme un matériau de qualité supérieure pour les cadres de vélo, car elle est solide, légère et relativement facile à fabriquer pour être très rigide dans une direction et souple dans une autre. Malgré sa popularité, ce matériau n'est pas très bien compris. Pourquoi est-il si cher ? Pourquoi a-t-il été inventé ? Est-il réparable ? Va-t-il détruire la planète ? Découvrons-le.
Pourquoi la fibre de carbone ?
La fibre de carbone est un matériau composite polyvalent qui permet aux concepteurs de vélos de développer des cadres aux qualités spécifiquement adaptées à des applications particulières. Ils peuvent être brillants sur le bitume, confortables en tout-terrain ou rapides comme des fusées sur la piste. Les vélos peuvent être conçus pour être principalement rigides et racés - mon vélo aérodynamique Specialized Venge est si rigide qu'il ne fléchit pratiquement pas - ou rapides mais confortables, comme le magnifique Bianchi Specialissima, un vélo d'endurance performant qui peut être utilisé pendant des jours.
Comme la fabrication de la fibre de carbone - communément appelée stratification - ne nécessite pas de joints disgracieux, les cadres peuvent également prendre des formes attrayantes et organiques, souvent dans le but d'obtenir des gains aérodynamiques. C'est le genre de matériau qui fait roucouler les gens.
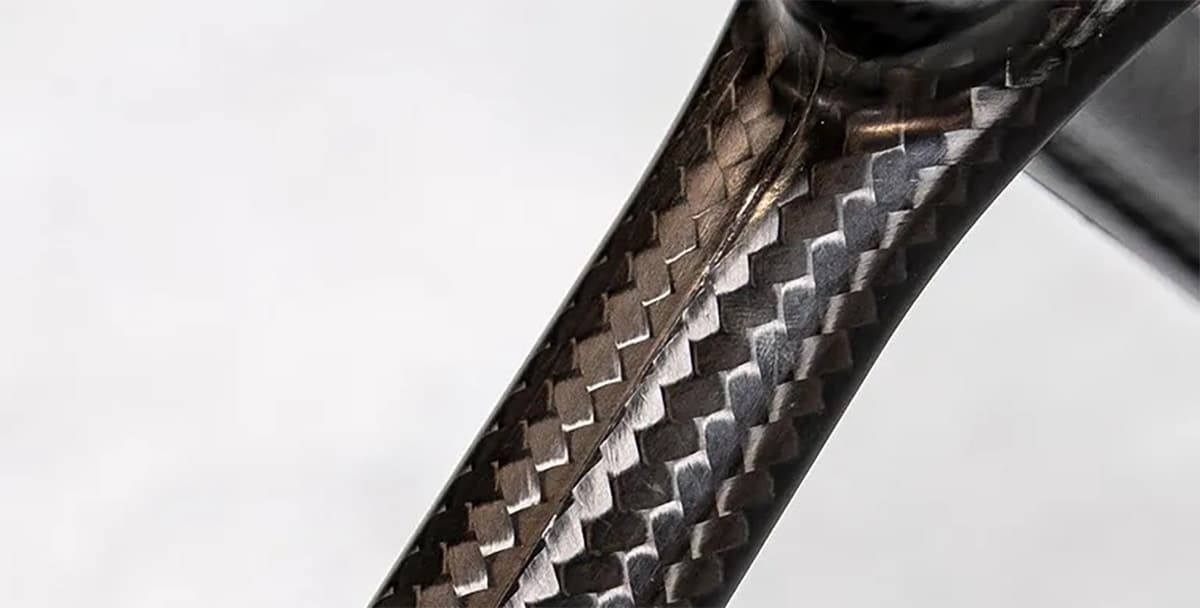
Pourquoi ce coût élevé ?
Il est indéniable que même les cadres en carbone d'entrée de gamme sont coûteux. Un vélo haut de gamme en fibre de carbone, tel que le Trek Madone SLR 9 Gen 7, peut vous coûter plus de $16 000/£13 000, dont au moins un tiers est imputable au cadre. Pourquoi ce prix élevé ?
"Il y a quinze ans, le coût de construction d'un cadre se répartissait entre un tiers de main-d'œuvre, un tiers de matériaux et un tiers de frais généraux, mais aujourd'hui, la main-d'œuvre est devenue la dépense la plus importante", explique Rob Gitelis, PDG de Factor Bikes. "Beaucoup d'entreprises ont délocalisé leurs usines de Chine vers l'Asie du Sud-Est parce qu'elles recherchent une main-d'œuvre moins chère.
Le coût des matériaux a également augmenté. La fibre de carbone étant fabriquée à partir de pétrole, son prix a augmenté dans le contexte des récentes tensions au Moyen-Orient et des attaques maritimes en mer Rouge.
"Si l'on considère les années 2023 et 2024, le prix de la fibre de carbone a augmenté d'environ 16%", explique M. Gitelis. "Le pétrole est sans aucun doute un facteur très important, tout comme la demande des autres industries. La plupart du temps, nous sommes en concurrence avec l'industrie aérospatiale pour les matériaux, ce qui entraîne une hausse des prix."
Malgré cela, M. Gitelis estime qu'il est peu probable que les hausses de prix soient répercutées sur le consommateur dans l'immédiat.
"Je pense qu'un grand nombre de fabricants de fibres de carbone chercheront à augmenter leurs prix, mais les marques devront les absorber car la concurrence est très forte en ce moment. Il y a beaucoup de stocks qui posent problème".
Le coût du carbone dépend également du type ou de la qualité de la fibre utilisée.
"Les coûts dépendent d'un grand nombre de facteurs, du prix du pétrole à la conception du cadre, mais aussi des fibres utilisées et de leur degré de raffinement", explique Sam Pendred, ingénieur concepteur chez Hope.
"Pour nos cadres de piste, nous utilisons la fibre de carbone la plus performante - à haut module - que l'on puisse trouver, qui était déjà chère de toute façon, mais qui continue d'augmenter. Mais si vous utilisez une fibre de module plus standard, c'est moins cher".
Selon Pendred, 100 g de fibre de carbone UD (unidirectionnelle) à haut module coûtent plus de 100 livres sterling par mètre carré, tandis que 300 g de fibre UD à module standard coûtent moins de 25 livres sterling. Environ sept mètres carrés sont utilisés dans le cadre d'une chenille Hope, dont la majeure partie est constituée de 100 g de fibre de carbone UD haut module, ce qui coûte à la marque environ 700 livres sterling en coûts de matériaux.
Qu'est-ce que la fibre de carbone ?
Étonnamment, pour ce qui est considéré comme un matériau de pointe, la fibre de carbone a été mise au point il y a plus de 160 ans, à l'origine pour être utilisée dans les ampoules à incandescence. Cependant, elle n'a pas suscité beaucoup d'enthousiasme jusqu'à ce que l'industrie aérospatiale reconnaisse son utilité dans les années 1960. Comme indiqué précédemment, il s'agit d'un sous-produit de l'industrie pétrolière.
"La fibre de carbone est fabriquée à partir du goudron de base des raffineries de pétrole, c'est essentiellement de la boue", explique Rob Granville, directeur de Carbon Bike Repair.
"Cette boue est séparée en deux types de carbone : le carbone bon marché, qui ressemble à un substitut de l'amiante et agit comme du ciment, et le carbone plus fin appelé carbone polyacrylonitrile (PAN).
"C'est ce carbone qui est ensuite purifié, à l'aide de la chaleur, et ce processus permet d'obtenir du graphite, qui est le premier matériau utilisable. Il est ensuite chauffé à nouveau pour obtenir ce que nous appelons le carbone à bas module, qui est le matériau utilisé pour la plupart des bicyclettes. En le chauffant à nouveau et en y ajoutant d'autres produits chimiques, on obtient du carbone haut module, qui est très solide et très rigide, mais incroyablement fragile".
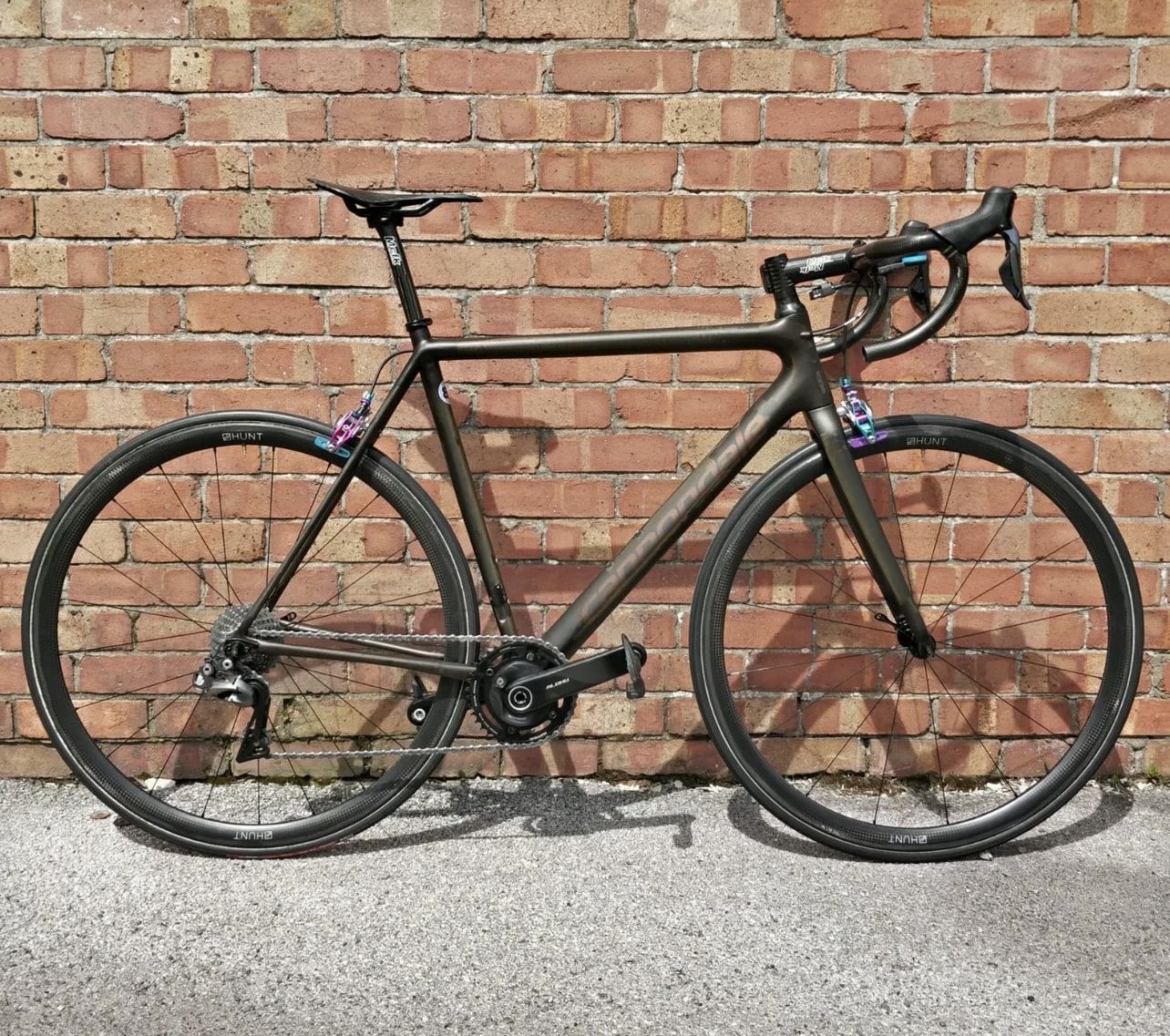
"Au cours du processus de chauffage, les fibres PAN sont essorées à plusieurs reprises pour éliminer tout l'oxygène, puis chauffées à nouveau à très haute température pour les carboniser et les débarrasser de toutes les impuretés", ajoute Chris Clarke, expert en composites à Hope.
"Ce qui reste, ce sont de fins filaments dont la largeur est environ dix fois inférieure à celle d'un cheveu humain. Ces filaments sont regroupés pour former ce que l'on appelle l'étoupe, qui est ensuite enroulée sur une bobine. Les fibres sont tissées en un tissu qui est imprégné d'une résine époxy pour les coller ensemble, créant ainsi des feuilles de fibres de carbone thermodurcies pré-imprégnées.
"La raison pour laquelle nous utilisons le pré-imprégné est que nous pouvons prédire avec précision la quantité de résine par rapport à la fibre que nous obtenons, ce qui est important lorsque vous essayez de prédire la résistance et la rigidité".
Comment sont fabriqués les cadres en carbone ?
Pour fabriquer un cadre de bicyclette, des feuilles de fibre de carbone pré-imprégnée sont découpées et superposées dans un moule. La façon dont les feuilles sont disposées, à la fois en épaisseur et en direction, influencera les propriétés du cadre final, permettant de régler à volonté la rigidité, la résistance et la compliance.
"L'une des qualités de la fibre de carbone, qui la rend si attrayante pour les fabricants de vélos, est qu'il est possible de dissimuler l'ADN de la construction d'un cadre dans la stratification", explique M. Granville. "Personne ne peut savoir combien de couches composent le cadre, à l'exception du concepteur.
"Une fois les couches superposées, le cadre est placé dans un four géant appelé autoclave, où il est chauffé jusqu'à ce que l'époxy contenu dans les couches se ramollisse suffisamment pour les lier ensemble. Pour éviter que le cadre ne s'effondre vers l'intérieur, des vessies en forme de ballon sont placées stratégiquement dans les tubes.
"Du point de vue de la conception, la fibre de carbone offre des possibilités infinies, car un cadre peut prendre presque n'importe quelle forme. Je pense que les concepteurs de notre industrie comptent parmi les meilleurs créateurs travaillant avec les composites aujourd'hui, plus encore qu'en Formule 1. Oui, les possibilités qu'offre la fibre de carbone aux concepteurs sont infinies, mais ils doivent toujours travailler dans des limites strictes - poids, puissance, règles de l'UCI et ce que le marché supportera en termes de performance, d'esthétique et de coût.
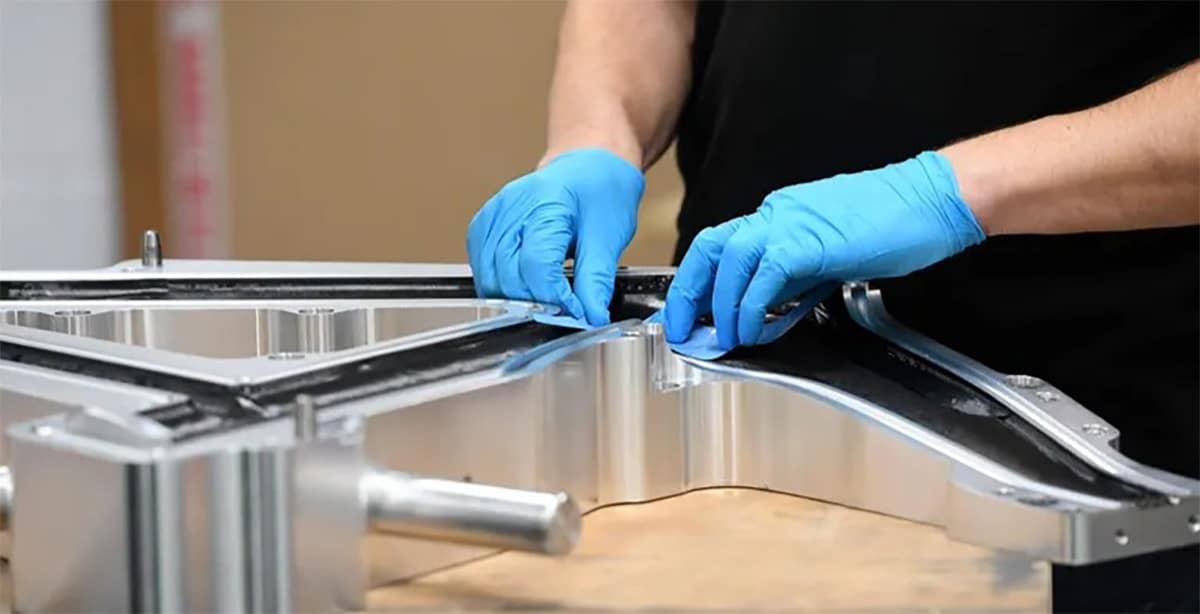
Un cadre en carbone réparé est-il sûr ?
De nombreux coureurs pensent à tort que la fibre de carbone ne peut pas être réparée, même s'il est vrai que la réparation d'un cadre en carbone n'est pas toujours simple.
"Après toutes ces années, je m'étonne que certaines personnes ne sachent pas que le carbone peut être réparé", déclare M. Granville.
"Il est vrai que les vélos modernes sont presque irréparables à la main. Si vous ne disposez pas d'une machine capable de simuler le moule dans lequel le vélo est sorti, la compression du carbone, l'épaisseur de la paroi du carbone et le profil du cadre, vous ne pouvez pas garantir la réparation sans couper le vélo en deux pour le vérifier. De nos jours, il faut de la technologie pour fabriquer un vélo et de la technologie pour le réparer.
"La fibre de carbone est réparable à l'infini, à condition que l'on puisse placer du carbone sur du carbone et qu'ils se lient. Sachant qu'il est impossible de tester jusqu'à la destruction, les seules choses qu'il n'est pas judicieux de réparer sont les parties d'un cadre qui sont à la fois uniques et critiques sur le plan structurel. Par exemple, pouvez-vous imaginer que votre pivot de fourche se brise au pied de votre tube de direction ? Vous vous retrouveriez face contre terre. Il en va de même pour le guidon, en particulier à l'endroit où la potence se fixe.
La fibre de carbone est-elle durable ?
En tant que sous-produit de l'industrie pétrolière et dépendant d'un processus de fabrication qui consomme beaucoup d'énergie, il est difficile de considérer la fibre de carbone comme un matériau durable.
"Les principaux problèmes environnementaux liés à la fibre de carbone sont le processus de production et les déchets à la fin de la durée de vie du produit", explique Erik Bronsvoort, fondateur de Circular Cycling.
"L'énergie nécessaire à la fabrication des fibres et les émissions de CO2 qui y sont associées sont énormes. Pour chaque kg de fibres de carbone produit, 20 kg de CO2 sont émis. Et ce, avant qu'elles ne soient mélangées à de la résine et transformées en produit.
"Les déchets en fin de vie sont également problématiques. La plupart des fibres de carbone thermodurcies utilisées dans les vélos ne peuvent pas être recyclées. Elle finit dans une décharge ou, pire encore, est brûlée dans un incinérateur, où la résine fond ou brûle, mais où la température est trop basse pour brûler les fibres, qui se retrouvent dans les cendres. Ces cendres sont ensuite souvent utilisées comme produit "vert" dans la construction des routes, ce qui ne fait qu'aggraver la situation à l'avenir.
"Chaque marque et chaque créateur doit assumer la responsabilité des produits qu'il met sur le marché. Cela va des droits du travail dans la chaîne d'approvisionnement à la déforestation, en passant par l'utilisation de l'énergie, la longévité des produits, les possibilités de réparation et les déchets. L'impact de notre système économique linéaire sur notre planète ne peut plus être ignoré, et il ne suffit pas d'attendre que les gouvernements ou les consommateurs fassent ce qu'il faut."
Comment Bronsvoort voit-il l'avenir de la fibre de carbone ?
"Plus les entreprises prendront conscience de l'impact de la fibre de carbone, plus elles commenceront à innover pour trouver des solutions de remplacement", explique M. Bronsvoort.
"Par exemple, j'ai vu des développements très intéressants dans les composites à base de biofibres dans les secteurs de la voile et de l'automobile. Je pense donc que nous verrons davantage de biocomposites recyclés à l'avenir, la fibre de carbone thermodurcissable traditionnelle étant réservée aux pièces très haut de gamme qui en ont vraiment besoin.
Le thermoplastique est-il une solution ?
Le composite de carbone thermoplastique gagne du terrain en tant qu'alternative plus durable à la fibre de carbone thermodurcissable, mais cette réputation est-elle méritée ?
"Une partie de l'initiative mondiale sur les déchets consiste à supprimer le processus thermodurcissable, car il produit des matériaux, comme la fibre de carbone, qui peuvent être réutilisés", explique M. Granville.
"En conséquence, l'industrie des composites se tourne vers la fibre de carbone thermoplastique comme alternative. Le thermoplastique est un plastique standard, comme le nylon ou le polypropylène, qui est broyé et peut être fondu plusieurs fois. Cette matière plastique est versée sur des brins de carbone, comprimée et pressée jusqu'à ce qu'elle soit complètement incorporée. Lorsqu'il est sec et prêt pour la fabrication, un autre morceau de carbone est posé dessus, prêt à être chauffé davantage jusqu'à ce que les matériaux fondent et se lient, ce qui donne un composant thermoplastique.
"Si, par la suite, le produit est découpé, le matériau peut être réutilisé en le réchauffant, ce qui permet de réduire considérablement les déchets. Les premiers produits que nous avons vus fabriqués à partir de thermoplastique, ou de plastique de fusion comme certains l'appellent, ont été des roues de vélo de montagne parce qu'elles sont plus douces à conduire, offrant un peu de suspension. Le thermoplastique est intéressant, mais sa rigidité n'est pas aussi efficace que celle du thermodurcissable, de sorte que les fabricants ont du mal à fabriquer des cadres aussi fins et aussi légers.
Pour Bronsvoort, la question n'est pas non plus tranchée.
"Les thermoplastiques offrent la possibilité de récupérer les fibres en faisant fondre la résine, mais je n'ai pas vu de preuve que ces fibres puissent être utilisées pour fabriquer à nouveau le même produit - en général, on observe un 'downcycle' au lieu d'un 'recycle' car les fibres deviennent plus courtes", déclare Bronsvoort.
"Par ailleurs, comment les consommateurs reconnaissent-ils qu'un produit est un thermoplastique recyclable ? Comment le produit se retrouve-t-il dans une installation disposant de la technologie nécessaire pour le recycler ? Ces facteurs de logistique inverse liés aux consommateurs sont difficiles à surmonter.
Ou s'agit-il de fibres d'origine végétale ?
Le fabricant de carbone Toray a obtenu la certification lui permettant d'utiliser la biomasse pour produire et fournir de la fibre de carbone à partir de la fin 2023, mais on ne sait pas exactement ce que ces matériaux contiennent. Toray n'a pas répondu à la demande de commentaire de Cycling Weekly, et nous nous sommes donc tournés vers Chris Clarke, de Hope, pour obtenir un pronostic.
"Les fibres d'origine végétale sont envisagées", explique M. Clarke. "Le lin a déjà fait l'objet d'essais, mais il était difficile à fabriquer et n'était pas très résistant. Mais il existe une matière appelée lignine, que l'on pense pouvoir carboniser à la place du pétrole à l'avenir.
"La lignine est un polymère qui remplit les espaces entre les fibres de cellulose dans les parois cellulaires des plantes, ce qui les rend rigides. On la trouve principalement dans les plantes ligneuses, telles que les arbustes et les arbres, et elle est largement répandue."
Selon des recherches sur la fibre de carbone durable à base de lignine, le remplacement de la fibre de carbone traditionnelle par de la fibre de carbone à base de lignine permet de réduire le potentiel de réchauffement planétaire de la production de 54%.
Mais tout le monde n'est pas convaincu.
"Presque n'importe quel tissu ou textile peut être transformé en matériau de substitution de la fibre de carbone si vous le mélangez à une résine qui durcit sous une forme solide", explique M. Gitelis.
"Nous avons vu des matériaux à base de chanvre, de bambou, mais rien n'a les mêmes propriétés de rigidité que la fibre de carbone. L'une des choses que nous obtenons de la fibre de carbone et que nous n'obtenons d'aucun autre matériau, c'est la caractéristique de rigidité. C'est cette qualité qui fait un bon cadre de vélo".
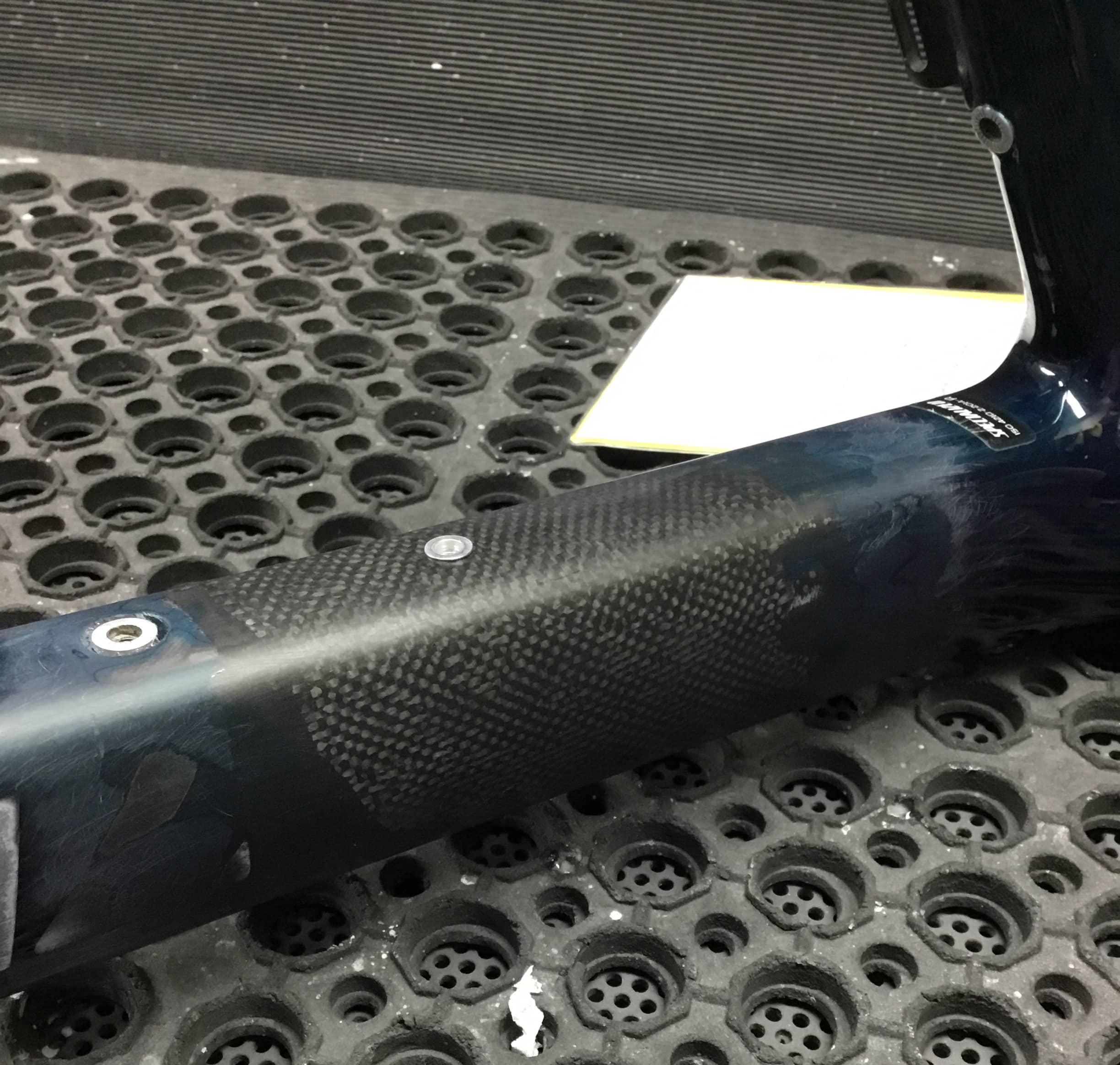
Le bilan
La fibre de carbone est un matériau remarquable qui nous permet de rouler sur des vélos esthétiques, légers et exaltants qui procurent une sensation de conduite comme aucun autre matériau. L'énorme demande de cadres en fibre de carbone est donc compréhensible.
Mais le paysage de la fibre de carbone est multiforme, avec un flot de défis en matière de conception, d'innovation, d'économie et d'environnement. Il est évident que l'on s'intéresse de plus en plus à rendre le matériau plus durable, et j'espère pour ma part que nous pourrons trouver des solutions respectueuses de l'environnement qui amélioreront le matériau et notre plaisir général de faire du vélo.
Crédit photographique : Emma Cole de Cycling Weekly
Autres études de cas